Адитивні технології: застосування 3D-друку в космічній галузі
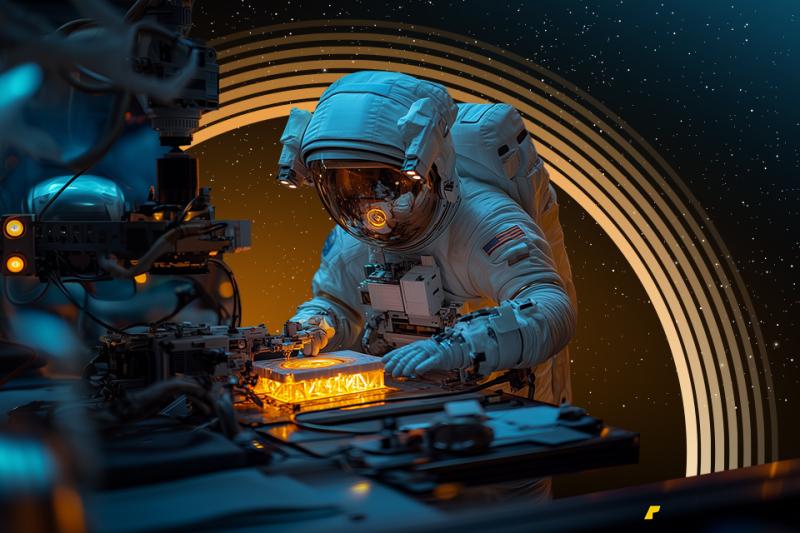
Створено Ольгою Авраміді та Олександром Бурлакою
Адитивні технології характеризуються тим, що матеріал не видаляється, а додається при створенні виробів. Найпоширенішим прикладом таких технологій є 3D-друк. Їхнє застосування можливе навіть у виготовленні ракет і космічних апаратів.
3D-друк -- одна з форм технологій адитивного виробництва, де тривимірний об'єкт створюється шляхом накладання послідовних шарів матеріалу за даними цифрової моделі. Останніми роками він розглядається як основний метод виготовлення деталей складної форми.
Цей процес також відомий як "вирощування", оскільки виріб формується поступово, шар за шаром. В залежності від застосованої технології, створення об'єкта може проходити знизу вгору або зверху вниз.
Основна відмінність від механічної обробки полягає в тому, що деталь формується шляхом "додавання" матеріалу. Натомість традиційна механічна обробка здійснюється шляхом "віднімання" зайвого матеріалу від заготовки. Після обробки зайвий матеріал перетворюється на стружку, що призводить до нижчого коефіцієнта використання матеріалу (КВМ).
Тривимірний друк включає в себе не одну, а цілу низку різноманітних технологій, об'єднаних спільною концепцією пошарового додавання матеріалу. Кожна з цих технологій здатна працювати з певними типами матеріалів і має свої унікальні переваги та обмеження.
Мабуть, найрозповсюдженішим типом 3D-друку є технологія FDM (Fused Deposition Modeling). У ній формування деталі відбувається методом натоплення, коли кожен наступний шар створюється з рідкого пластику, що пропускається через екструдер.
Більшість домашніх 3D-принтерів функціонують саме за цим принципом. Порівняно з іншими технологіями, цей метод є надзвичайно простим. Основне завдання полягає в подачі пластикової нитки до нагрівальної головки.
Для FDM можна застосовувати майже будь-які недорогі термореактивні полімери, які твердіють при зниженні температури. Хоча вироби, створені таким способом, не вирізняються значною міцністю, вони є надзвичайно економічними і дозволяють легко надати їм будь-якої форми.
Наступною технологією 3D-друку є SLM/DMP (Selective Laser Melting / Direct Metal Printing). Вона призначена для виготовлення виробів з металу. Звичайно, тримати їх у повністю розплавленому стані у великій кількості й у такому вигляді подавати через формувальне сопло достатньо проблематично.
Отже, на практиці використовується альтернативний підхід. Метал перетворюють на порошок і насипають його шарами. Потім, високопотужний лазер точково діє за 3D-моделлю, розплавляючи матеріал і створюючи суцільну структуру.
Таким чином можна отримати достатньо складні й при цьому стійкі до різних механічних, хімічних та температурних впливів вироби та деталі. Саме цей метод зазвичай використовується для виготовлення робочих частин різноманітних агрегатів. Недоліком його є висока складність та енерговитратність технології.
Якщо ж у процесі пошарового спікання застосовується не метал, а твердий пластик, то таку технологію називають вибірковим лазерним спіканням (SLS).
За допомогою лазерної установки та сканувального дзеркала промінь лазера спрямовується на необхідні ділянки порошку, спікаючи їх разом шар за шаром. Після спікання першого шару вирівнювальний механізм додає тонкий шар порошку поверх нього, і процес відбувається повторно до повної побудови об'єкта. Тобто відтворення об'єкта відбувається знизу вгору, а за рахунок заповнення камери порошком не потрібна побудова підтримувальних структур.
На відміну від SLM/DMP, SLS характеризується меншою потужністю лазера та значно простішим режимом його використання. Однак це призводить до суттєвого зниження міцності виготовлених виробів.
Іншим видом 3D-друку є MJP (MultiJet Printing), що дозволяє багатоструминний друк з використанням воску або фотополімеру.
Ці матеріали тверднуть під дією ультрафіолетового випромінювання. Тож саме ним і закріплюють кожен шар після нанесення. В іншому технологія проста: друкувальною головкою на робочу платформу шар за шаром наноситься матеріал (або їх поєднання).
Кожен шар відповідає окремому рівню в заданій 3D моделі. "Р родзинка" методики полягає в кількості сопел, яка може варіюватися від кількох одиниць до сотень. Завдяки цим соплам стає можливою одночасний друк з різних матеріалів, які можуть значно відрізнятися за щільністю, в'язкістю та іншими властивостями.
В цілому, такий підхід дозволяє друкувати дуже швидко та отримувати матеріали з попередньо заданою структурою. Недоліком є відносно висока вартість матеріалів. Тим не менш, цей метод залишається другим за популярністю після FDM.
Деталі, надруковані методом MJP
MJF (Multi Jet Fusion) -- це технологія 3D-друку з використанням поліаміду, де нагрівальний елемент одночасно впливає на всю робочу площину. Отримані деталі за зовнішнім виглядом нагадують вироби, створені методом SLS.
Процес друкування полягає в нанесенні першого шару поліаміду на робочу поверхню. Потім у визначених координатах цього шару розподіляють зв'язувальну речовину. Принтер впливає на шар інфрачервоним випромінюванням, внаслідок чого покритий зв'язувальною речовиною порошок спікається. Після цього накладається наступний шар поліаміду, і процедура повторюється. Виріб формується поступово, шар за шаром, доки не буде повністю готовий.
SLA (Laser Stereolithography) -- всередині 3D-принтера міститься ванна з рідким фотополімером. Поверхнею матеріалу рухається лазерний промінь, і там, де він торкається рідини, фотополімер застигає, створюючи шар виробу.
Ця техніка схожа на технологію SLS 3D-друку, проте замість порошку використовується рідкий фотополімер. В решті, процес являє собою послідовне нарощування шарів для створення об'єктів на основі параметрів 3D-моделі.
CJP (ColorJet Printing) — це метод кольорового 3D-друку, який базується на склеюванні гіпсового порошку.
Технологія CJP використовує порошкоподібні матеріали, окремі ділянки яких з'єднуються за допомогою сполучної речовини. Спочатку на робочу платформу наноситься шар порошку, що відповідає висоті першого шару. Зазвичай, всі шари моделі мають однакову висоту. Порошок вирівнюється валиком, а надлишки видаляються. Далі, друкувальна головка подає сполучну речовину на ділянки, що відповідають перерізу першого шару. Після цього робоча платформа опускається вниз на висоту одного шару, і наноситься новий шар матеріалу. Процес повторюється: сполучна речовина подається на ділянки, відповідаючи наступному шару. Усі етапи тривають до повної побудови об'єкта.
В цілому, на підприємствах 3D-друк застосовують для таких завдань:
1. Швидке створення початкових прототипів.
2. Масове виготовлення робочих компонентів.
Найрозповсюдженіший метод для отримання прототипів -- це FDM-принтери. Вони дешеві, ними наповнений ринок, тому вони є майже на кожній фірмі. SLA-принтери використовують рідше, але вони дозволяють отримувати якісніші прототипи. CJP-друк можна віднести як до гібриду друку для прототипів так і декоративного.
Для масового виготовлення деталей зазвичай застосовують технології SLM/DMP, SLS, MJF та MJP. Сьогодні 3D-друк активно інтегрується в різні сфери, включаючи медицину, будівництво та текстильне виробництво, де експериментують з новими матеріалами.
Кожен вид 3D-друку має свої конкретні переваги та недоліки, на які треба орієнтуватися при виборі методу для своїх потреб. Задач, які хочуть розв'язати за допомогою 3D-друку, з кожним днем стає все більше, тому весь час розробляють нові методи 3D-друку та обладнання.
Якщо провести порівняння деталей, створених традиційними методами, такими як фрезерування або лиття, з елементами, виготовленими за технологією 3D-друку, то можна визначити наступні переваги та недоліки кожного з підходів.
Розглянемо спочатку недоліки:
Попри певні недоліки та відносну новизну цієї технології, 3D-друк користується великою популярністю в сучасному виробництві завдяки численним перевагам:
Застосування 3D-друку в ракетобудуванні можливе скрізь, єдине обмеження -- це габарити робочих зон сучасних принтерів. Важливо також правильно підібрати метод адитивного виробництва, врахувавши умови роботи кожної деталі та вимоги до неї.
Слід зауважити, що 3D-друк не призначений для заміни всіх методів виробництва. Деякі критично важливі компоненти космічної техніки, наприклад, трубопроводи, які функціонують під тиском, не можуть бути виготовлені цим методом.
Що стосується електроніки, то тут 3D-друк також застосовується для створення друкованих плат. Існує кілька основних підходів до використання адитивних технологій при їхньому виготовленні:
Найскладнішим елементом ракети з точки зору конструкції й виготовлення є двигун, тому застосування 3D-друку варто починати з нього. Наявні технології мають обмеження щодо міцності деталей, які за їхньою допомогою можуть виготовлятися. Тому сьогодні ще не часто можна зустріти надруковані деталі, які працюють під тиском (такі як балони чи трубопроводи), оскільки структура деталей не є цілком монолітною, бо створена шарами, то збитковий тиск може призвести до руйнування.
3D-друк широко застосовується для виготовлення окремих компонентів ракет у багатьох компаніях. Наприклад, SpaceX використовує 3D-принтери для створення деяких деталей двигуна.
NASA здійснила успішні випробування ракетного двигуна, виготовленого за допомогою 3D-друку, досягнувши нового рівня в розробці інноваційної силової установки під назвою Rotating Detonation Rocket Engine (RDRE). Інженери з Центру космічних польотів імені Маршалла в Хантсвіллі, штат Алабама, успішно протестували нову модель RDRE, створену за технологією 3D-друку, протягом 251 секунди (понад чотири хвилини), генеруючи тягу понад 5800 фунтів. RDRE представляє собою значний прорив в ефективності проєктування.
Компанія Agnikul Cosmos (Індія) запустила ракету з надрукованим двигуном Agnibaan SOrTED (Suborbital Technological Demonstrator) -- це перша ракета, запущена з приватного стартового майданчика, це перший у країні політ із напівкріогенним двигуном і перший у світі однокомпонентний двигун, надрукований на 3D-принтері, розроблений і виготовлений місцевими мешканцями.
Orbex Space замовляє найбільший промисловий 3D-принтер у Європі для швидкого налагодження ракетобудування. Очікується, що таким чином невдовзі щорічно виготовлятиметься 35 ракетних двигунів і турбонасосів.
Orbex доручила AMCM створити найбільший у Європі промисловий 3D-принтер, що дозволить британській інноваційній космічній компанії швидко самостійно виготовляти складні ракетні двигуни. Цей спеціалізований 3D-принтер великого об'єму дасть змогу Orbex щорічно виробляти понад 35 великомасштабних ракетних двигунів і турбонасосних систем для основного ступеня, що допоможе компанії збільшити свої виробничі потужності для майбутніх запусків.
Фірма Relativity Space пішла далі й намагається зробити повністю друковану ракету.
Технологія 3D-друку для Terran R стратегічно застосовується для зниження складності транспортного засобу та підвищення його технологічності. Компанія продовжує зосереджуватися на нових горизонтах великомасштабного адитивного виробництва після успішного підтвердження ефективності 3D-друкованих ракет з Terran 1.
Незважаючи на те, що технології 3D-друку вже неодноразово застосовувалися для виготовлення різних компонентів, організація виробництва космічних ракет за допомогою цих технологій є складнішим завданням, ніж може здаватися на перший погляд. Головною перешкодою на шляху до реалізації такого виробництва є розміри деталей.
Зазвичай адитивні технології використовуються для створення об'єктів, розміри яких вимірюються у міліметрах і сантиметрах. Однак, компоненти ракет можуть досягати довжини від кількох десятків сантиметрів до метрів. Тому робочий простір, в якому здійснюється формування таких деталей, має бути навіть більшим.
Це, у свою чергу, вимагає переосмислення конструкції всього 3D-принтера, використання більш потужних електродвигунів та збільшення його ваги. В результаті отримуємо значний промисловий пристрій.
До того ж, якщо товщина шару матеріалу лишається тією самою, то при збільшенні розмірів деталі, час її виготовлення виходить дуже значним. Виникає питання, чи може 3D-принтер весь цей час працювати у безперервному режимі, чи йому знадобиться технологічна перерва. А якщо вона таки має відбутися, то як це вплине на міцність зчеплення матеріалу в шарі, що формується, з тим, який затверднув ще кілька годин тому.
Не слід забувати, що деталі, створені за допомогою 3D-принтера, потребують зняття з нього та транспортування по цеху. Це означає, що використання підіймально-транспортного обладнання залишається необхідним.
Оптимальне місце для встановлення 3D-принтера, який виробляє компоненти для ракет, – це діюче авіакосмічне підприємство. Розташування його у випадковому місці не є ефективним, оскільки дана техніка потребує спеціалізованої промислової інфраструктури.
Усе це не означає, що адитивні технології неможливо використовувати у виробництві космічної техніки. Навпаки. Вони можуть справді полегшити його, особливо там, де мова про створення абсолютно нових зразків. Проте справа ця не така проста, як здається.